This page contains descriptions of what kind of materials I use for many of my projects.
They are all different to work with, and have certain characteristics for use.
One of the most fascinating parts of this craft is to find and use different rare, natural and synthetic materials,
and mix them in different ways, to either create for a stronger product or something aesthetically creative.
Read through, and maybe you find the knife that suits your needs.
Wood.
Many of the species of wood I use are natural and with natural color. If I use any surface color, this is stated in the description for each knife. Natural wood has an oil finish. There are several kinds of oil, with more or less the same characteristics. This is the traditional way of surface treating knifehandles in Norway. I never use any laqueur, since this might peel off after several years of use. All my products are made to last, and the shine are only from sanding to a very high grit, and then polished with different kinds of wax for each material.
Wooden handles are not as cold in the winter, as synthetics or ivory.
I use wood from all over the world, and do my best to ensure that they are all from respectable sources.
The blocks on the right are stabilized with blue, or clear color.
The pieces of wood are carefully selected to have either a certain density of pattern, or the right lines to follow the curves.
Read more about the stabilizing process further down the page.
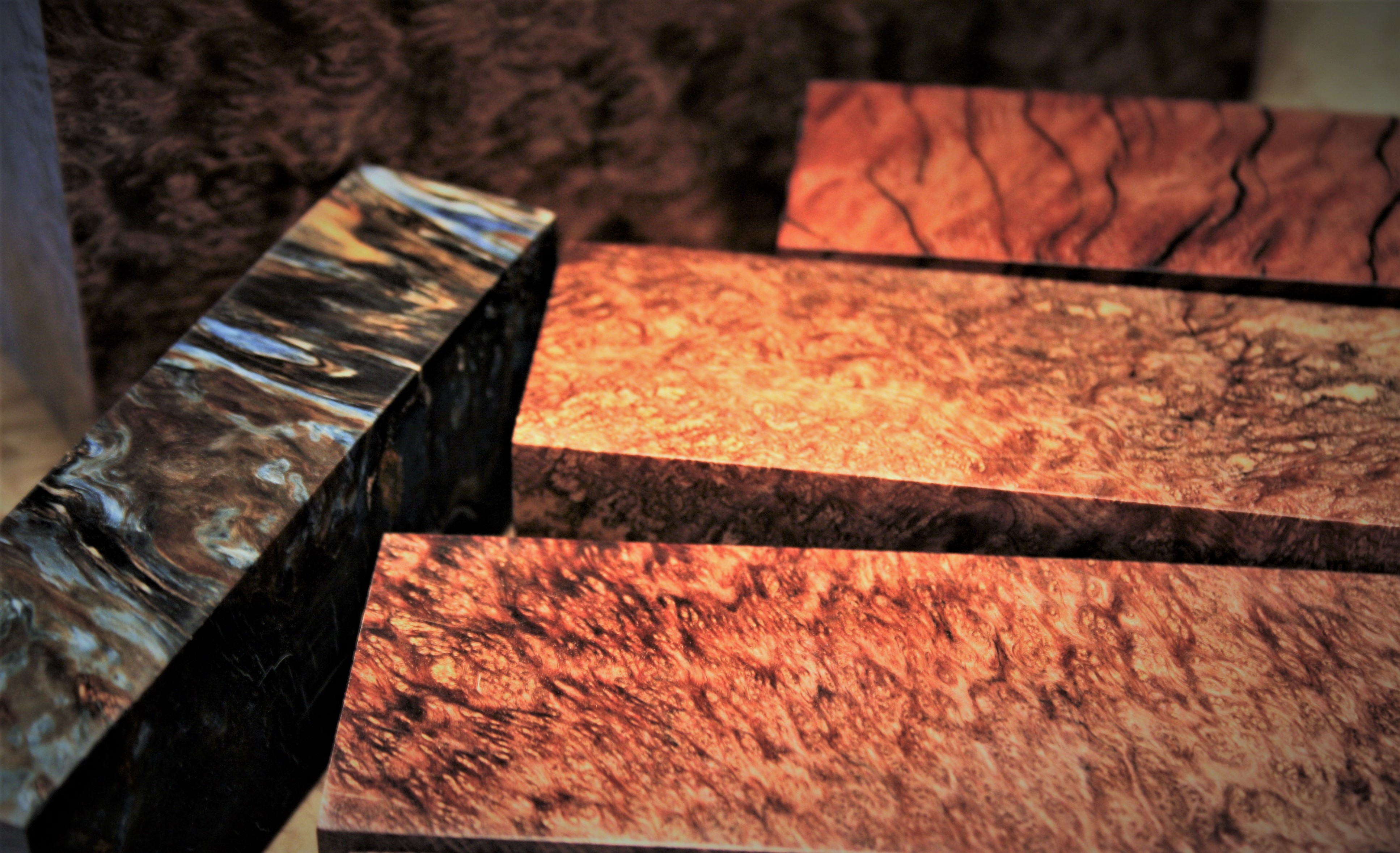
Bone, horns and antlers.
A traditional material for knifehandles are bones or antlers.
I often use buffalo horn, with its dark black color. They might also have some white stripes along the marrow. Buffalo horn can get a very high shine. But you have to be careful when polishing it, since it doesnt like heat.
Moose and reindeer antler are also used, and some other fossil bones which has been stabilized. If I use bones and antlers, I prefer to use stabilized or only very special quality material without pores in the marrow. This makes it at lot easier to keep clean, and to have a nicer surface for a long time. Reindeer antler are often more grey in color, and a lot thinner in size.
The knife on the right is made of buffalo horn and has a whale tooth bolster.
This material needs very little care, and lasts for ages as a using knife. One of my regular knives for fishing are made of buffalo horn. I recommend a knife with more curves for better grip, rather than one that is more shaped like a barrell if you need it for a wet environment.
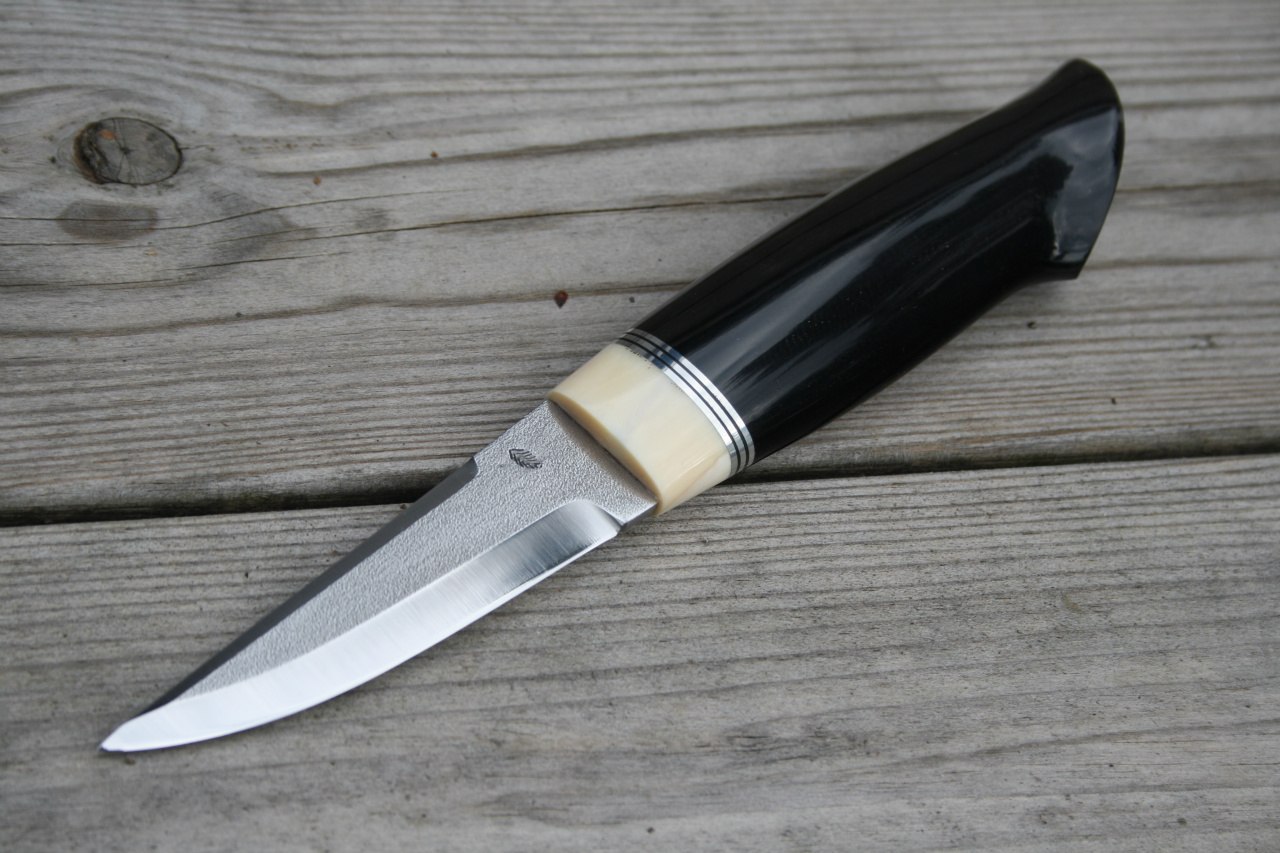
Mammoth ivory and tooth.
Mammoth ivory and their teeth are some of my favourite materials.
They range from white, brown, blue and dark grey colors, depending on what kind of soil or ice they have been lying in. Lots of the materials have been stabilized, especially the teeth. Some of the ivory can be used in the natural condition. Most of my fossil knives are made to be used, but is adviced to be taken a bit better care of. If you drop a knife with a whole handle of ivory, it is more likely to be damaged, compared to a knife of natural wood. These knives will be a little colder during the winter, if you are looking for something to bring fishing.
When you look at the patterns on the ivory, they are usually crosscut, or cut lenght wise. When you see round rings going from the middle of the handle and outwards, this is the cross section of the ivory. It looks in a way like the surface rings of a tree. The most usual way to cut ivory is along the length, making for larger handles, and you will see stripes along the handle.
The teeth are full of enamel. This makes them extremely tough to work with, and most knifemakers stay away from using them. These cannot really be compared to the other materials because of their toughness. They require a lot of extra work to be able to get a nice finish.
The fossils are usually assumed to be between 20.000 and 40.000 years old.
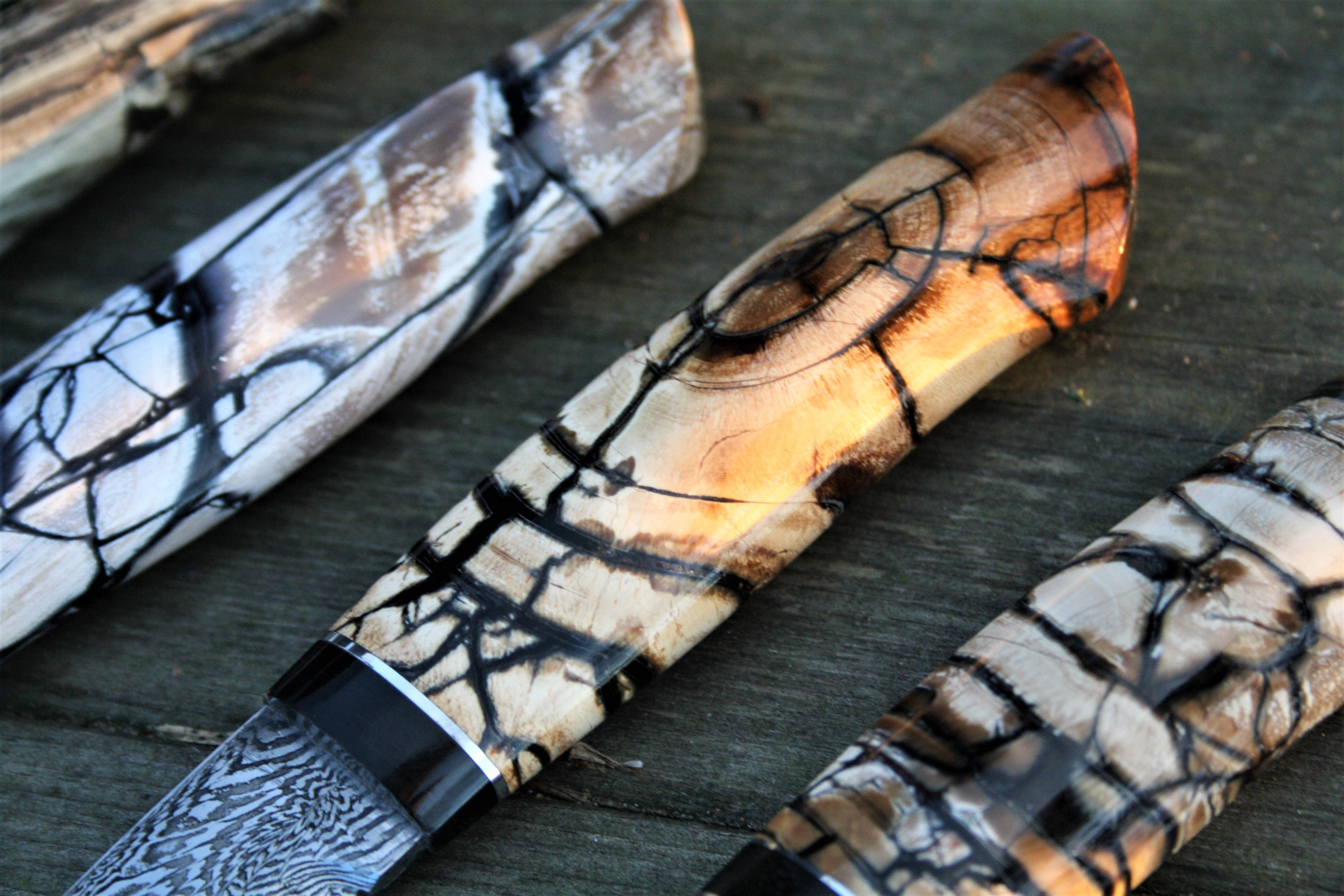
Synthetic.
There are lots of new modern materials which are made of different synthetic resins.
Acrylics, epoxy based, etc, makes for a possibility to make items with a completely different kind of look, and mixing a lot of colors and patterns. This is not the traditional way to make knives, but it has become more and more popular the recent years. These materials are less prone to react to temperatures, and require very little care after using.
Mixed with stainless steel, you have a knife that is also very suited for those who doesn't take as much care of a knife.
The knife on the right is made with cast aluminium shreds and corn leaves.
All handles of synthetic material are shaped in the same way as other materials,
from a large block, and sanded to finish. It is different from wood, and cannot be carved with a knife.

Pearls and corals.
Some of natures finest materials.
Pearls are shells, and come in many different colors. Coral can also have large variations in color and pattern.
Some of the most difficult materials to work with, since the pieces are usually thin or brittle.
Mostly used for artknives, and I only use of the highest quality. Usually seen as inlays in the back of the knives
or for bolsters on ivoryknives. The deep shimmer of colors can almost seem magical, and are highly sought after.
The knife on the right has blacklip mother of pearl as a bolster, one of the rarest of pearls.
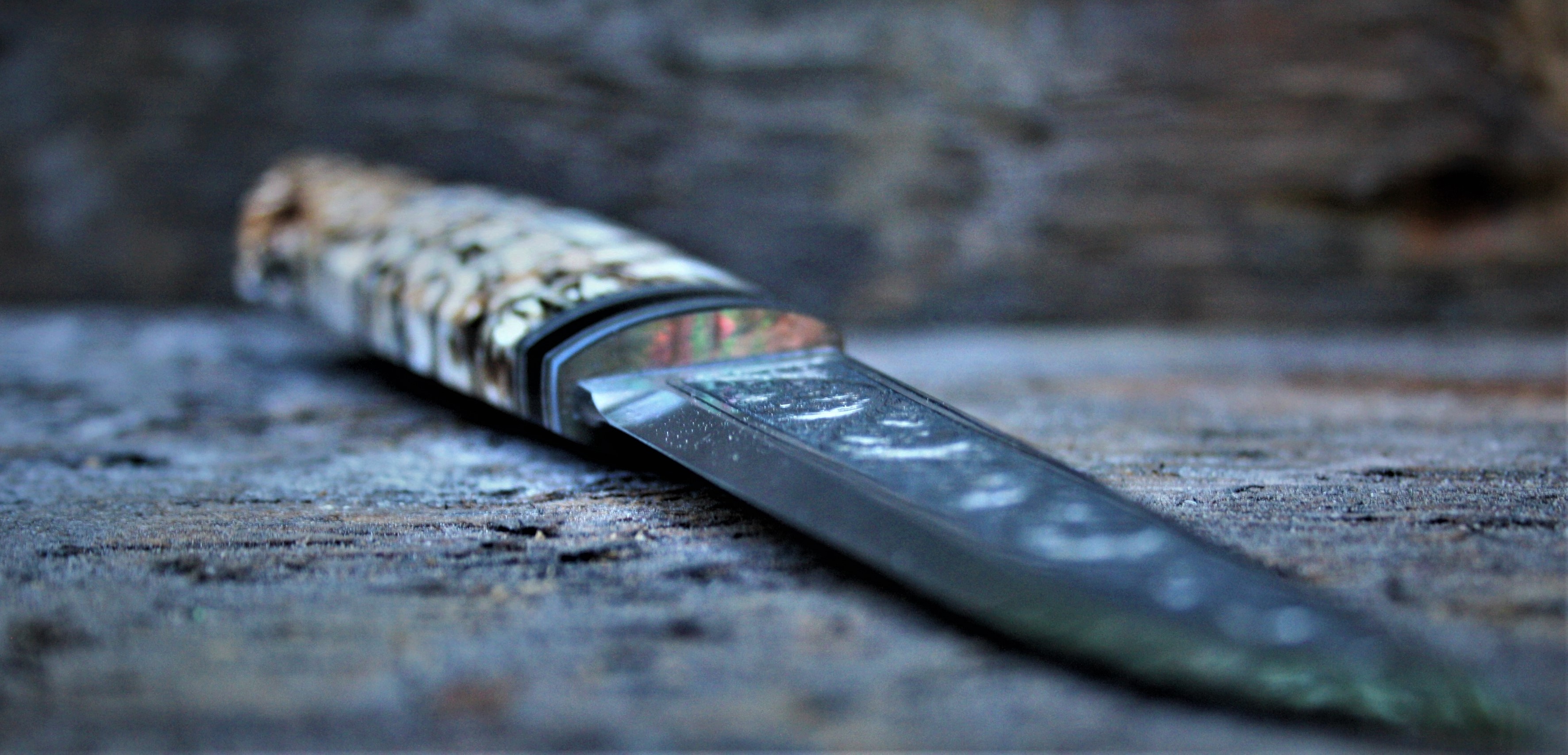
Leather.
Most of my knives come with a sheath made of leather.
There are many kinds of leather, suitable for different styles of knives, and decorations.
I use almost exclusively rawhide leather.
This is very strong, which have a raw sentre, making a very hard sheath.
It needs to be carefully cut, and measured for shrinkage. It has to be hand sewn, and you cant use a machine.
Rawhide leather is suitable for a technique called "pauting", in Norwegian. This is a decoration method
where you use pressure to make folds, or different layers in leather, such as acantus. This leather cant have cut/carved decor.
Mostly I use a thickness of 2.2-2.5mm. You wont get as deep decor as with thicker leather,
but the sheath will be more elegant, and less bulky.
The straps are made of a softer leather, more suitable to give the right freedom of movement when the knife is on the belt.
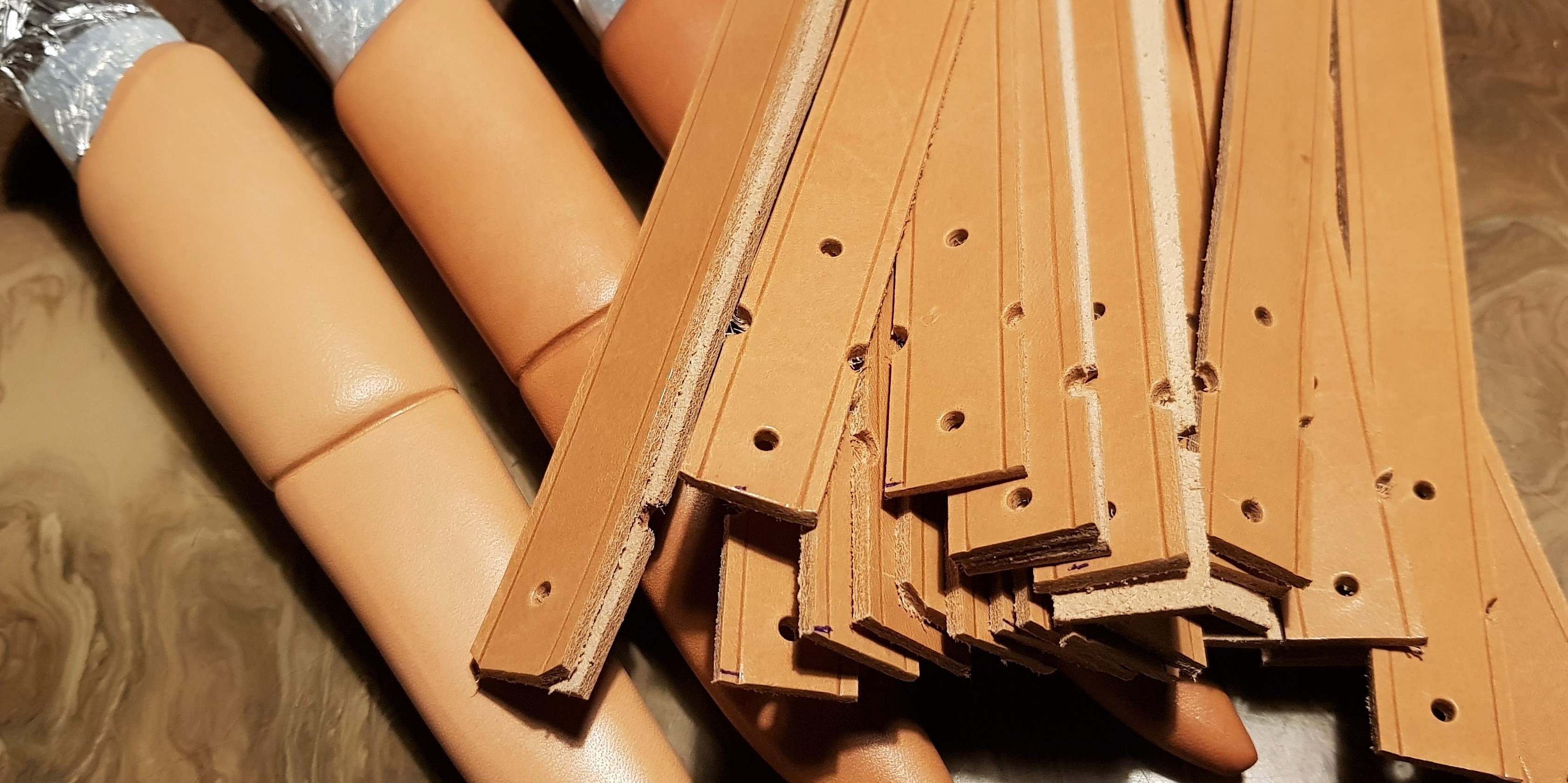
Steel and other metals.
All my blades are made of high quality steel.
I make many of the blades myself, but I also buy blades from blacksmiths in scandinavia.
They might be laminated, or in one piece of stainless steel.
Many of my expensive knives are made from stainless damascus, or patternwelded, mosaicdamascus.
Therefore the patterns you see in the steel, are different kinds of steel, forgewelded together, then folded, twisted or turned, to make a special pattern. This pattern becomes visible when the blade is put in an acid after grinding.
The blades on the right are made of stainless powdersteel. The shiny one has been polished after etching.
My metal inlays in the handles are often a mix of pewter, or silver.
Pewter are easier to bend, and holds a nicer shine, and doesn't need any brushing up.
I might also use gold, but then for custom projects.
The pieces of chess that I make are mainly in bronze. I also use silver and copper in random projects.
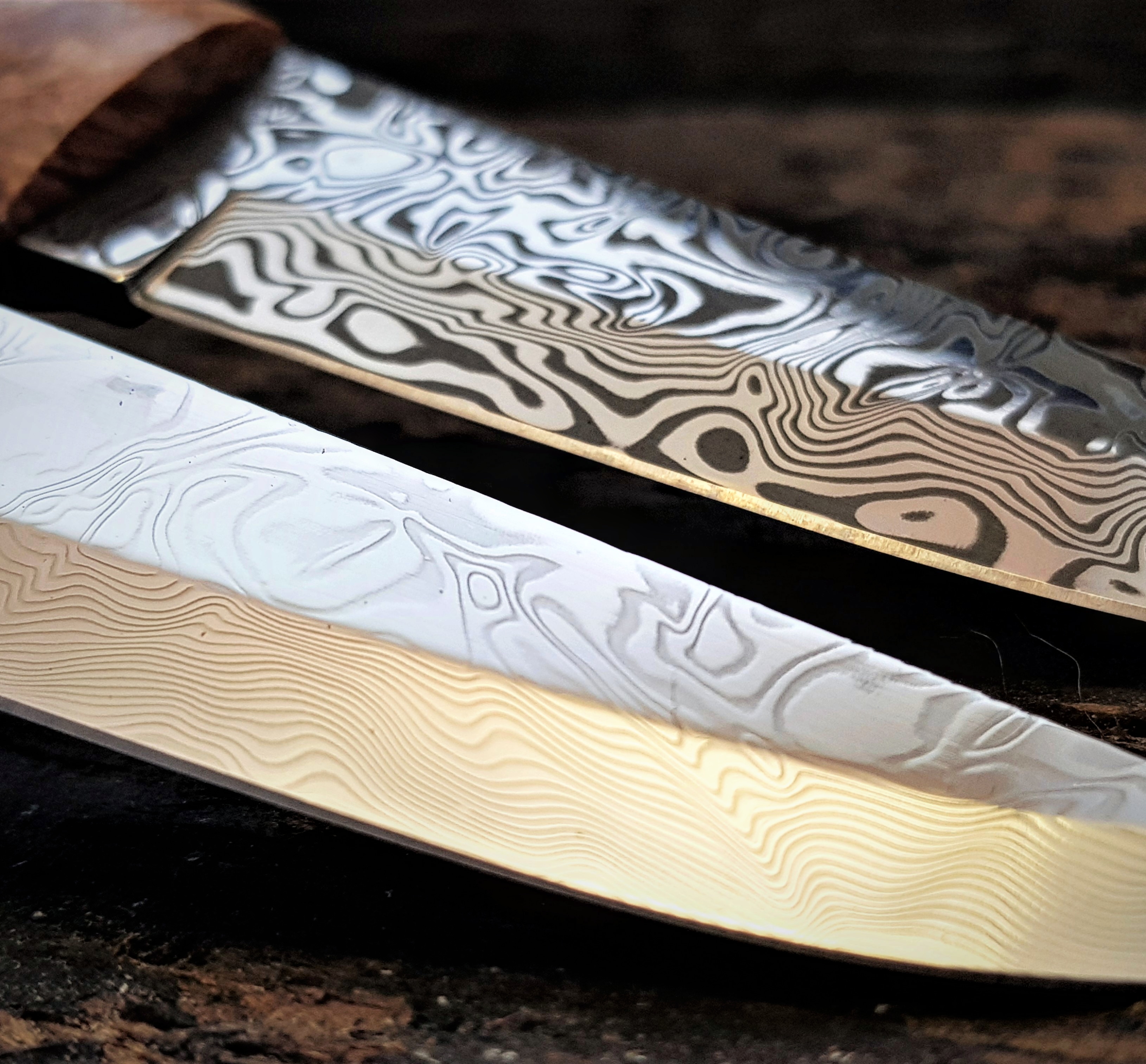
So what is stabilizing?
Materials are cleaned and dried to a very low humidity percentage.
Then they are filled with resin, making them stronger, filling voids, cracks and pores. Mostly wood that is beginning to rot get this treatment, like spalted birch.
All of this is done with heavy equipment for pressure or vacuum, and are hardened.
Special resins are used for the purpose, designed for each group of materials.
Some makers are doing this procedure at home, often giving an uneven result, or makes the handle still require some extra finish. All my stabilized materials are done by professionals.
The treatment is done before you make the knifehandle.
This gives the knifemaker a lot more work to shape the handle,
and can hardly be compared to working with natural wood.